除塵脫硫技術(shù)現(xiàn)狀:
我國(guó)電力部門(mén)在七十年代就開(kāi)始在電廠進(jìn)行煙氣脫硫的研究工作,先后進(jìn)行了亞鈉循環(huán)法(W-L法)、含碘活性炭吸附法、石灰石-石膏法等半工業(yè)性試驗(yàn)或現(xiàn)場(chǎng)中間試驗(yàn)研究工作。進(jìn)入八十年代以來(lái),電力工業(yè)部門(mén)開(kāi)展了一些較大規(guī)模的煙氣脫硫研究開(kāi)發(fā)工作,同時(shí),近年來(lái)我國(guó)也加入了煙氣脫硫技術(shù)的引進(jìn)力度。目前國(guó)內(nèi)主要的脫硫工藝有:
(1)石灰石-石膏濕法煙氣脫硫工藝
石灰石(石灰)-石膏濕法煙氣脫硫工藝主要是采用廉價(jià)易得的石灰石或石灰作為脫硫吸收劑,石灰石經(jīng)破碎磨細(xì)成粉狀與水混合攪拌制成吸收漿液。在吸收塔內(nèi),吸收漿液與煙氣接觸混合,煙氣中的二氧化硫與漿液中的碳酸鈣以及鼓入的氧化空氣進(jìn)行化學(xué)反應(yīng)被吸收脫除,終產(chǎn)物為石膏。脫硫后的煙氣依次經(jīng)過(guò)除霧器除去霧滴,加熱器加熱升溫后,由引風(fēng)機(jī)經(jīng)煙囪排放,脫硫渣石膏可以綜合利用。
(2)海水煙氣脫硫工藝
海水煙氣脫硫工藝是利用海水的堿度達(dá)到脫除煙氣中的二氧化硫的一種脫硫方法。煙氣經(jīng)除塵器除塵后,由增壓風(fēng)機(jī)送入氣一氣換熱器中的熱側(cè)降溫,然后送入吸收塔。在脫硫吸收塔內(nèi),與來(lái)自循環(huán)冷卻系統(tǒng)的大量海水接觸,煙氣中的二氧化硫被吸收反應(yīng)脫除。脫除二氧化硫后的煙氣經(jīng)換熱器升溫,由煙道排放。洗滌后的海水經(jīng)處理后排放。
(3)爐內(nèi)噴鈣加尾部增濕活化工藝
爐內(nèi)噴鈣加尾部增濕活化工藝(簡(jiǎn)稱LIFAC工藝)是在爐內(nèi)噴鈣脫硫工藝的基礎(chǔ)上在鍋爐尾部增設(shè)了增濕段,以提高脫硫效率。該工藝多以石灰石粉為吸收劑,石灰石粉由氣力噴入爐膛850-1150度溫度區(qū),石灰石受熱分解為氧化鈣和二氧化碳,氧化鈣與煙氣中的二氧化硫反應(yīng)生成亞硫酸鈣。由于反應(yīng)在氣固兩相之間進(jìn)行,收到傳質(zhì)過(guò)程的影響,反應(yīng)速度較慢,吸收劑利用率較低。在尾部增濕活化反應(yīng)人,增濕水以霧狀噴入,與未反應(yīng)的氧化鈣接觸生成Ca(OH)2進(jìn)而與煙氣中的二氧化硫反應(yīng),進(jìn)而再次脫除二氧化硫。當(dāng)Ca/S為2.5及以上時(shí),系統(tǒng)脫硫率可達(dá)到65%-80%。煙氣脫硫后,由于增濕水的加入煙氣溫度下降(只有55-66度),一般控制出口煙氣溫度高于露點(diǎn)10-15度,增濕水由于煙溫加熱被迅速蒸發(fā),未反應(yīng)的吸收劑、反應(yīng)產(chǎn)物呈干燥態(tài)隨煙氣排出,被除塵器收集下來(lái)。由于脫硫過(guò)程對(duì)吸收劑的利用率低,脫硫副產(chǎn)物是以下穩(wěn)定的亞硫酸鈣為主的脫硫灰,副產(chǎn)物的綜合利用受到的影響。
(4)電子束煙氣脫硫工藝
是一種物理方法和化學(xué)方法相結(jié)合的高新技術(shù)。本工藝的流程是由排煙預(yù)除塵、煙氣冷卻、氨的沖入、電子束照射和副產(chǎn)品捕集工序組成。鍋爐所排出的煙氣,經(jīng)過(guò)集塵器的粗濾處理之后進(jìn)入冷卻塔,在冷卻塔內(nèi)噴射冷卻水,將煙氣冷卻到適合于脫硫、脫硝處理的溫度(約70度)。煙氣的露點(diǎn)通常經(jīng)為50℃,被噴射呈霧狀的冷卻水在冷卻塔內(nèi)得到蒸發(fā),因此,不產(chǎn)生任何廢水。通過(guò)冷卻塔后的煙氣流進(jìn)反應(yīng)器,在反應(yīng)器進(jìn)口處將的氨氣、壓縮空氣和軟水混合噴入,加入氨的量取決于SOX和NOX濃度,經(jīng)過(guò)電子束照射后,SOX和NOX在自由基的作用下生成中間物硫酸和硝酸。然后硫酸和硝酸與共存的氨進(jìn)行中和反應(yīng),生成粉狀顆粒硫酸銨和硝酸銨的混合體。反應(yīng)所生成的硫酸銨和硝酸銨混合微粒被副成品集塵器所分離和捕集,經(jīng)過(guò)凈化的煙氣升壓后向大氣排放。
(5)循環(huán)流化床鍋爐脫硫工藝(鍋爐CFB)
循環(huán)流化床鍋爐脫硫工藝是近年來(lái)迅速發(fā)展起來(lái)的一種新型燃煤燃燒脫硫技術(shù)。其原理是燃料和作為吸收劑的石灰石粉送入燃燒室中部送入,氣流使燃料顆粒、石灰石粉和灰一起在循環(huán)流化床強(qiáng)烈擾動(dòng)并充滿燃燒室,石灰石粉在燃燒室內(nèi)裂解成氧化鈣,氧化鈣和二氧化硫結(jié)合成亞酸酸鈣,鍋爐燃燒室溫度控制在850度左右,以實(shí)現(xiàn)反應(yīng)佳。
(6)雙堿法煙氣脫硫工藝
雙堿法是先用可溶性的堿性清液作為吸收劑吸收SO2,然后再用石灰乳或石灰對(duì)吸收液進(jìn)行,由于在吸收和吸收液處理中,使用了兩種不同類型的堿液,故稱為雙堿法。
在雙堿法中應(yīng)用多的方法是以燒堿(NaOH)、純堿(NacO3)或亞硫酸鈉(Na2sO3)吸收SO2,然后,吸收液用石灰。后的鈉堿溶液返回洗滌系統(tǒng)用作吸收液,后生成的亞硫酸鈣或硫酸鈣沉淀,經(jīng)處理后拋棄或回收。鈉鈣雙堿法是較為常見(jiàn)的脫硫方法之一。
脫硫方案確定
鍋爐為煤粉燃燒方式,硫含量在0.8%。
根據(jù)當(dāng)?shù)氐呐欧乓螅瑹煔庵械亩趸蚺欧艥舛葢?yīng)控制在800mg/m3以下,煙塵濃度控制在200 mg/m3。要求安裝的除塵脫硫裝置應(yīng)具有90%的脫硫效率,98%以上的除塵能力。
(1)現(xiàn)有煙氣脫硫技術(shù)分析及本工程技術(shù)方案選取
任何一種煙氣脫硫技術(shù)都是包括脫硫工藝和脫硫設(shè)備兩部分組成的。所謂的脫硫工藝就是指采用的何種脫硫方法,它包括所用的脫硫原料,脫硫過(guò)程參數(shù)如何控制以及終所形成的脫硫副產(chǎn)物等。而脫硫設(shè)備則是指為煙氣與脫硫液提供相互接觸傳質(zhì)的設(shè)備。
(2)幾種煙氣脫硫工藝方法簡(jiǎn)評(píng)
目前有效的二氧化硫控制方法仍為對(duì)鍋爐燃燒后的煙氣進(jìn)行脫硫處理,其中濕法煙氣脫硫因其具有技術(shù)成熟、脫硫效率等特點(diǎn),因此在世界上得到廣泛應(yīng)用,目前已安裝的煙氣脫硫設(shè)備中有80%以上都屬于濕法煙氣脫硫技術(shù)。
濕法煙氣脫硫方法也分很多種,其中以利用石灰石或石灰的鈣基濕法較為常用。
石灰石(石灰)-石膏濕法煙氣脫硫工藝主要是采用廉價(jià)易得的石灰石或石灰作為脫硫吸收劑,石灰石經(jīng)破碎磨細(xì)成粉狀與水混合攪拌制成吸收漿液。當(dāng)采用石灰作為吸收劑時(shí),石灰粉經(jīng)消化處理后加水?dāng)嚢柚瞥晌諠{液。在吸收塔內(nèi),吸收漿液與煙氣接觸混合,煙氣中的二氧化硫與漿液中的碳酸鈣以及鼓入的氧化空氣進(jìn)行化學(xué)反應(yīng)被吸收脫除,終產(chǎn)物為石膏。脫硫后的煙氣依次經(jīng)過(guò)除霧器除去霧滴,加熱器加熱熱升溫后,由引風(fēng)機(jī)經(jīng)煙囪排放,脫硫渣石膏可以綜合利用。
氨法煙氣脫硫技術(shù)方法也廣受重視,該法所得到的脫硫副產(chǎn)硫酸銨可作肥料出售,具有較好的經(jīng)濟(jì)效益。然而,氨法脫硫技術(shù)通常存在的問(wèn)題有由于氨的腐蝕性較強(qiáng),對(duì)設(shè)備及管道腐蝕嚴(yán)重。另外,為了保證脫硫率,脫硫溶液中的氨水濃度需要維持再較高水平,這樣在氣液接觸過(guò)程中,容易導(dǎo)致大量的氨氣揮發(fā)進(jìn)入煙氣中,造成氨的逃逸損失。同時(shí),逃逸到煙氣中的氨還很容易與煙氣中殘留的二氧化硫作用,在煙氣中形成難以捕集的銨鹽氣溶膠粒子,導(dǎo)致嚴(yán)重的二次污染。這些問(wèn)題地限制了氨法脫硫技術(shù)的實(shí)際推廣。
鎂法脫硫技術(shù)也是很有前途的一種濕法脫硫技術(shù)。該技術(shù)自1975年被開(kāi)發(fā)以來(lái)在日本、等發(fā)達(dá)逐步得到推廣,并逐漸成為鈣基脫硫的取代工藝之一。鎂法脫硫技術(shù)具有脫硫效率高、不易結(jié)垢、設(shè)備緊湊、脫硫液對(duì)設(shè)備腐蝕性低等優(yōu)點(diǎn)。因而,該方法近年來(lái)得到廣泛重視。然而,目前該方法所存在的問(wèn)題有:脫硫劑的高溫方法較復(fù)雜過(guò)程耗能量過(guò)高。若將副產(chǎn)物作為硫酸鎂回收,則存在副產(chǎn)物銷路問(wèn)題,且脫硫過(guò)程需要不斷補(bǔ)充新的鎂基原料,使脫硫成本增加。
為克服上述問(wèn)題,我們分別開(kāi)發(fā)出了鈉-鈣雙堿法和鎂-氨雙堿法兩種脫硫工藝。前者是為了解決石灰或石灰石作為脫硫劑時(shí)的吸收效率不高及結(jié)垢等問(wèn)題,所得到的脫硫產(chǎn)物仍為石膏;后者則較好地克服了單獨(dú)用氨的脫硫過(guò)程中氨的損失、腐蝕及二次污染問(wèn)題,且終可以回收硫酸銨,實(shí)現(xiàn)硫的資源化利用。
脫硫方法 | 石灰/石灰石法 | 氨法 | 鎂法 | 鎂-氨雙堿法 | 鈉-鈣雙堿法 |
脫硫塔體積 | 適中 | 小 | 較小 | 較小 | 小 |
所需的脫硫劑 | 石灰/石灰石 | 氨水 | 氧化鎂等 | 氧化鎂、氨水 | 鈉堿及石灰 |
消耗的脫硫劑 | 石灰/石灰石 | 氨水 | 氧化鎂等 | 氨水 | 石灰 |
脫硫產(chǎn)物 | 石膏 | 硫酸鎂 | 硫酸鎂 | 硫酸銨 | 石膏 |
脫硫率 | 高 | 高 | 高 | 高 | 高 |
腐蝕問(wèn)題 | 較輕 | 明顯 | 較輕 | 較輕 | 很好 |
系統(tǒng)能耗 | 中 | 中 | 中 | 中 | 中 |
是否易結(jié)垢 | 偶然 | 下游煙道 | 否 | 否 | 否 |
二次污染問(wèn)題 | 無(wú) | 明顯 | 少 | 少 | 少 |
工藝經(jīng)濟(jì)性 | 好 | 好 | 一般 | 好 | 很好 |
工藝介紹
1.脫硫塔工作原理
煙氣進(jìn)入噴淋脫硫塔筒體,由塔底進(jìn)入,經(jīng)密集的噴淋霧化層,煙氣與液體霧粒逆流充分接觸,在霧粒降落過(guò)程中吸收SO2 并捕潤(rùn)塵粒,濕潤(rùn)的塵粒向下流入脫硫塔底部,從溢流孔排出進(jìn)入沉淀池。在筒體內(nèi)上升的凈化后的氣體經(jīng)過(guò)氣水分離器除霧脫水,完成整個(gè)除塵脫硫程序,之后通過(guò)筒體上部錐體部分引出。含塵廢液通過(guò)筒體底部溢流孔排入沉淀池,(溢流孔有水封設(shè)計(jì)防止漏氣,并設(shè)有清理孔便于進(jìn)行筒體底部清理)經(jīng)沉淀(除灰)并加堿)后循環(huán)使用。
2.脫硫液雙堿法工作原理
脫硫液采用外循環(huán)吸收方式,循環(huán)池內(nèi)一次性加入碳酸鈉制成脫硫液(循環(huán)水),用循環(huán)泵打入脫硫塔進(jìn)行除塵脫硫。吸收了SO2的脫硫液落入塔底流入池,與新來(lái)的石灰漿液進(jìn)行反應(yīng),反應(yīng)后的漿液流入沉淀池沉淀,當(dāng)一個(gè)沉淀池沉淀物集滿時(shí),漿液切換流入到另一個(gè)沉淀池,然后由人工或用潛污泵清理這個(gè)池沉淀的沉渣,廢渣晾干后外運(yùn)處理。上清液流入循環(huán)池,循環(huán)池內(nèi)經(jīng)和補(bǔ)充新鮮堿液的脫硫液還是由循環(huán)泵打入脫硫塔,經(jīng)噴嘴霧化后與煙充分接觸,然后流入池,如此循環(huán),循環(huán)池內(nèi)脫硫液PH下降到程度后則補(bǔ)充新鮮堿液,以恢復(fù)循環(huán)脫硫液的吸收能力。
雙堿法理論上只消耗石灰,不消耗鈉堿,但是由于脫硫渣帶水會(huì)使脫硫液損失一部分鈉離子,再加上煙氣中的氧氣會(huì)將部分Na2SO3氧化成Na2SO4(在循環(huán)噴淋過(guò)程中,Na2SO4不能吸收SO2),故需在循環(huán)池內(nèi)補(bǔ)充少量純堿或廢堿液。
基本化學(xué)原理可分為脫硫過(guò)程和過(guò)程兩部分。
在塔內(nèi)吸收SO2
Na2CO3+SO2=Na2SO3+CO2 (1)
Na2SO3+SO2+H2O=2NaHSO3 (2)
2NaOH+SO2=Na2SO3+H2O (3)
其中式(1)是啟動(dòng)階段純堿溶液吸收SO2反應(yīng)方程,式(2)是運(yùn)行過(guò)程的主要反應(yīng)式,式(3)是液PH較高時(shí)的主要反應(yīng)式。
用消石灰
Ca(OH)2+Na2SO3+1/2H2O=2NaOH+CaSO3•1/2H2O
Ca(OH)2+2NaHSO3=Na2SO3+CaSO3•1/2H2O+3/2 H2O
在石灰漿液(石灰達(dá)到達(dá)飽和狀況)中,NaHSO3很快與Ca(OH)2 反應(yīng)從而釋放出[Na+],[SO32-]與[Ca2+]反應(yīng),反應(yīng)生成的CaSO3以半水化合物形式沉淀下來(lái)從而使[Na+]得到。Na2CO3只是一種啟動(dòng)堿,起動(dòng)后實(shí)際上消耗的是石灰,理論上不消耗純堿(只是清渣時(shí)會(huì)帶也一些,被煙氣中氧氣氧化會(huì)有損失,因而有少量損耗),的NaOH和Na2SO3等脫硫劑循環(huán)使用。
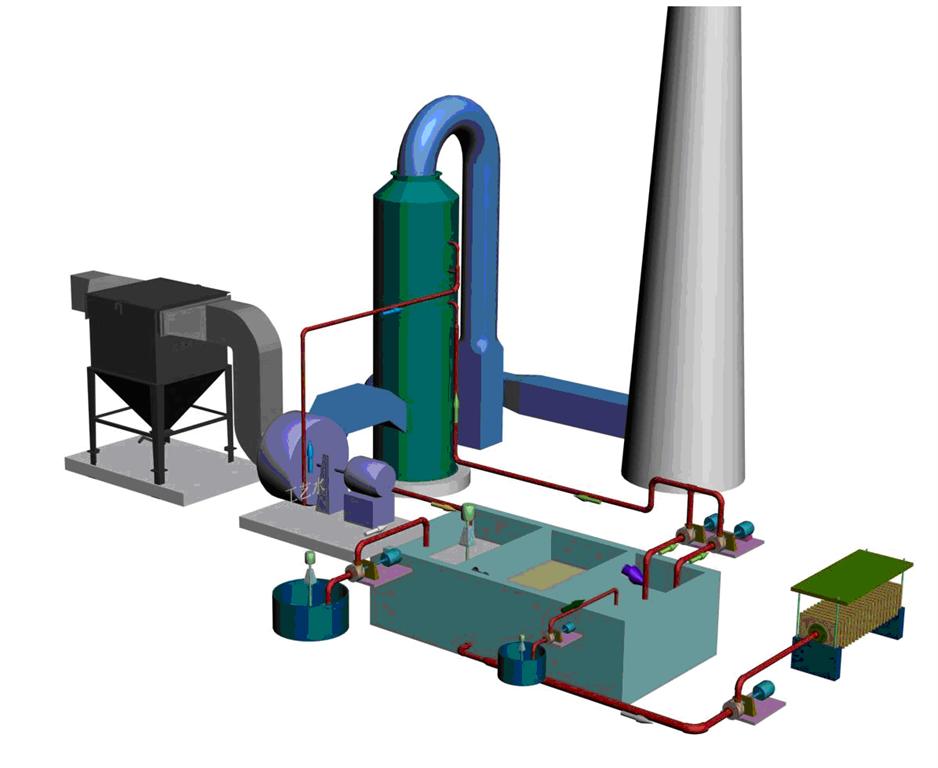
工藝特點(diǎn)
與其它脫硫工藝相比,噴淋霧化脫硫工藝原則上有以下優(yōu)點(diǎn):
1)、 運(yùn)用旋流射流技術(shù)、壓力霧化技術(shù),設(shè)備阻力小
2)、 用鈉堿液脫硫,循環(huán)水基本上是[Na+]的水溶液,在循環(huán)過(guò)程中對(duì)水泵、管道、設(shè)備均無(wú)腐蝕與堵塞現(xiàn)象,便于設(shè)備運(yùn)行與保養(yǎng);
3)、 吸收劑的重生和脫硫渣的沉淀發(fā)生在塔外,這樣避免了塔內(nèi)堵塞和磨損,提高了運(yùn)行的可靠性,降低了操作費(fèi)用;
4)、 鈉基吸收液吸收SO2速度快,故可用較小的液氣比1:1-2,達(dá)到較高的脫硫效率;
技術(shù)特點(diǎn)
我公司已經(jīng)在多個(gè)項(xiàng)目上已經(jīng)應(yīng)用成熟的雙堿法噴淋霧化脫硫工藝技術(shù)。較之其它脫硫工藝,該工藝具有以下優(yōu)點(diǎn):
1)、具有佳的性價(jià)比。該工藝技術(shù)與國(guó)內(nèi)外其它脫硫技術(shù)相比脫硫效率達(dá)到93-97%,而且液氣比遠(yuǎn)遠(yuǎn)低于其它鈣法技術(shù)。具有工藝流程簡(jiǎn)單,投資省、綜合運(yùn)行成本低的特點(diǎn)。高濃度的煙氣脫硫后可以滿足SO2環(huán)保排放要求,并且煙氣含塵量進(jìn)一步減少,可以實(shí)現(xiàn)花錢(qián)少、辦實(shí)事的目的;
2)、該工藝在燃煤鍋爐的除塵脫硫項(xiàng)目中運(yùn)行效果非常好,這已從多個(gè)項(xiàng)目中得到了證實(shí);
3)、技術(shù)成熟,運(yùn)行可靠性高。該工藝技術(shù)煙氣脫硫裝置投入率為95%以上,系統(tǒng)主要設(shè)備很少發(fā)生故障,因此不會(huì)因脫硫設(shè)備故障影響正常生產(chǎn)系統(tǒng)的運(yùn)行;
4)、對(duì)操作彈性大,對(duì)煤種變化的適應(yīng)性強(qiáng)。該技術(shù)用堿液作為脫硫劑,工藝吸收效果好,吸收劑利用率高,可根據(jù)爐窯煤種變化,適當(dāng)調(diào)節(jié)pH值、液氣比等因素,以保證設(shè)計(jì)脫硫率的實(shí)現(xiàn);
5)、和沉淀分離在塔外,大大降低塔內(nèi)和管道內(nèi)的結(jié)垢機(jī)會(huì);
6)、鈉堿循環(huán)利用,損耗少,運(yùn)行成本低;
7)、正常操作下吸收過(guò)程無(wú)廢水排放;
8)、灰水易沉淀分離,可大大降低水池的投資;
9)、脫硫渣,溶解度極小,無(wú)二次污染,可考慮綜合利用;
10)、鈉堿吸收劑反應(yīng)活性高、吸收速度快,可降低液氣比,從而既可降低運(yùn)行費(fèi)用,又可減少水池、水泵和管道的投資;
11)、石灰作劑(實(shí)際消耗物),運(yùn)行成本低。
12)、可以用廢堿液作為脫硫劑,進(jìn)一步降低成本。
13)、工藝簡(jiǎn)單,比較適用于中小型工業(yè)鍋爐和爐窯配套使用。
系統(tǒng)實(shí)施后的煙氣排放技術(shù)指標(biāo):
二氧化硫排放濃度:≤200mg/Nm3
設(shè)備總脫硫效率:90%以上(滿足水量、水壓、水質(zhì)和藥量時(shí))